Handmade presian rug
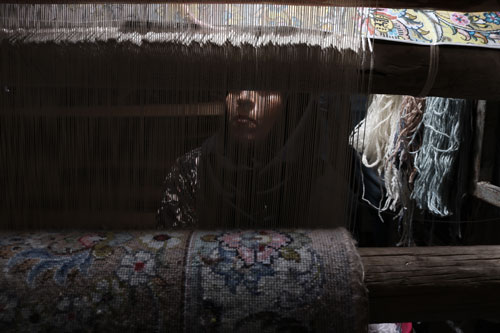
The first rug was possibly created by nomads to cover up the floor of their tents.
Step by step, men and women of family work together to prepare and create a rug.
In spring, sheep are washed extensively to remove dust and sweat of migration from their wool. Afterwards in a special ceremony, the sheep are sheared and women start folding the wool in a way that the lining is seen.
Spinning technique, amount of required twisting and diameter of string are then determined based on the type of rug, which can be Kilim, Jajim, Carpet, Gabbeh, Floor cover and Saddlebag.
White, clean and well-spun wool is separated and used later for delicate rugs such as kilim, Jajim, saddlebag that require thinner strings and better colors. Tougher and unorganized wool is also separated to be sold or to produce thicker strings which are used for thicker rugs and ropes. These wool are then spun, twisted and prepared for washing and coloring in the form of big skeins.
Once preparations are done, cauldrons are filled with water and boiled while Alum, color fixers and natural plants are used to produce the desired colors. Once the skeins are added, the cauldron must be stirred continuously to avoid burning the strings. Afterwards, they are washed and dried in several stages as to avoid merging colors upon weaving, dissolving upon washing the rug and to safeguard the hands of weavers.
Usually the most important color of a Persian rug is crimson which can be produced using various plants among which, rose madder or red seed are more popular than others.
At last, design process starts based on new and exclusive designs, dimensions, background color and rug pattern. After calculating margins and medallion, the rug is designed in a process called Black shade scheme.
As the design is completed, coloring and dotting begins.
Next stage is binding, mapping and then scaffold number of rug is written on the back of the map. The longest and most difficult part is weaving which includes two types:
- handmade
- hook-made